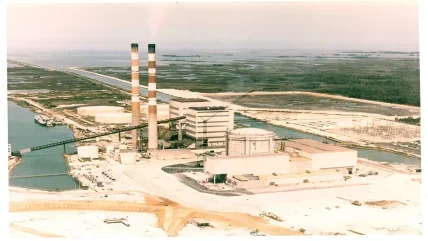
Orano Decommissioning Services recently completed the first cut to separate and then package the top third of the reactor pressure vessel (RPV) with its embedded internal components at unit 3 of the US Crystal River NPP. The work was carried out using Orano’s patented Optimised Segmentation (OS) process for the accelerated decommissioning project.
The Crystal River Nuclear Plant also called the Crystal River 3 (CR3) in Florida is currently being decommissioned. The 860 MWe pressurised water reactor plant began operation in 1976, and operated for 33 years until shutdown in 2009. It was permanently closed in 2013. Decommissioning was originally expected to take 50 years for completion by 2074, with dismantling starting in 2067.
By 2018, all used fuel had been transferred to an on-site Independent Spent Fuel Storage Installation and in 2020 the US Nuclear Regulatory Commission (NRC) approved transfer of the plant’s licence from Duke Energy to Accelerated Decommissioning Partners (ADP – a joint venture between NorthStar Group Services and Orano USA). The Florida Public Service Commission subsequently approved the transaction and ADP began decontamination and dismantlement later in 2020 instead of 2067.
It was the third plant built as part of the 4,700-acre Crystal River Energy Complex (CREC) which comprised a single NPP along with four fossil fuel power plants. The RPV will be cut into three segments as part of the accelerated decommissioning. Orano USA CEO Amir Vexler said the project is “on task, on time, on budget” after “safely cutting out and packaging an irradiated 246-tonne chunk of steel and material”.
As part of the OS process, Orano first cut up the RPV internals underwater and categorised them based on radioactivity, with the Greater-than-Class-C low-level waste (LLW) separated and packaged for long-term storage onsite. The remaining LLW was placed back into the reactor vessel in order to optimise transportation and disposal cost-effectiveness. Once the RPV was repacked and drained it was filled with an engineered grout that hardened and transformed it into a single, solid mass. To separate the top third of this structure into the first piece, Orano used diamond wire sawing to horizontally cut straight through the steel reactor vessel, solidified grout, and internals.
This first piece was lifted out of the reactor vessel cavity and transferred into an Orano-designed custom-built package, which the team filled with grout to immobilise the contents before welding it shut in preparation for transportation to disposal.
Reactor dismantling operations started at CR3 in 2021. Components of the reactor cooling system (steam generators, main coolant pumps and motors, the pressuriser, and large bore piping) have been removed from the containment building and shipped off-site for disposal. Segmentation of the reactor internals took place in 2022 and removal of all reactor structures from the containment building should be completed this year.
The accelerated decommissioning process involves removing, packaging, and shipping low-level radioactive materials, such as the RPV, to an off-site licensed disposal facility and then demolishing the reactor building. Non-radiological buildings and structures can be demolished at any time as the project progresses. Twenty-four-hour security, emergency response, and radiological and environmental monitoring programmes continue during and after the decontamination and dismantlement process is completed.
Once all the buildings have been cleared from the site, the only remaining structure will be the dry storage facility with the used nuclear fuel. The fuel will remain as a securely guarded facility until the it can be removed to a national used fuel repository or a consolidated interim storage facility (CISF) when either become available.