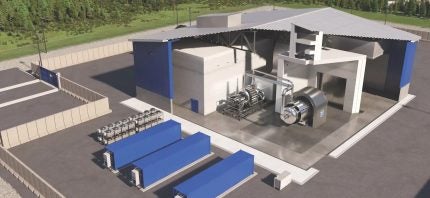
Westinghouse’s eVinci microreactor is a transportable 5 MWe nuclear power plant designed to be as versatile as possible. With multiple applications on the cards, the reactor could see its first deployment in Canada following an agreement with Saskatchewan Research Council to explore industrial, research and energy use applications. With C$80m (US$59m) in government funding to support licensing and other work for the project, the reactor is scheduled to be completed in 2029. Following a tie-in with Canadian firm Prodigy Clean Energy, the reactor is also being assessed and designed to be deployed commercially at the heart of a floating power station as a mobile power pack for multiple applications. Eddie Saab, Vice President eVinci Market Development and President at Westinghouse Electric Canada Inc, outlines the thinking behind the eVinci design: “Several years ago our engineers were assessing various technologies that would fit end uses for remote communities and off-grid applications for industrial customers who don’t have access to grid power. The engineers determined the heat pipe reactor technology which Los Alamos National Labs in the US had been using for creating electricity for the NASA space programme would be ideal.” He continues: “It was very small scale just using uranium to heat up heat pipes and converting that heat into electricity. Westinghouse licensed the technology and then went on an engineering research and development programme to scale that technology up to be commercially viable.”
That design programme has now resulted in the eVinci microreactor. In the eVinci unit, decay heat is removed via natural convection through air-to-air hear exchangers.
The core transfers heat to the heat tube canister which, Westinghouse says, provides reliable heat removal to the atmosphere using natural convection and without the need for operator actions. “Some of the attributes that we really liked was that the technology when fully operational actually has no moving parts. It doesn’t use any external water sources either,” he says.
This is one of the passive safety features of the design. The use of passive heat pipes rather than a liquid heat removal system eliminates the need for reactor coolant and associated systems as well as cooling water, simplifying the design and removing loss of coolant-type incidents from the equation. The system all doesn’t have any pumps and he machinery typically needed in a nuclear power plant or indeed any power plant that generates power from boiling water into steam.
Saab explains: “The rector itself is taking ambient air, heating up the air and then exhausting hot air into essentially a reverse jet engine. It’s a Brayton cycle power conversion unit. For customers who require just hot process heat you can do away with the power conversion unit and leverage the hot air. Typically, we’re going to see a need for both with some customers requiring high quality process heat for industrial applications, but also power generation for electricity. Using it for electricity, still provides about 7 MWth at about 1500C so there could be applications in a micro grid or a community or maybe a university where both 5 MW of electricity and about 7 MW of process heat is needed. Any process or industrial applications that require high temperature heat are suitable.”
Saab is keen to emphasise that the design team kept a keen focus on commercial considerations, saying: “There needs to be a sweet spot between the output and the cost for it to be commercially valid and that’s the balance that they’ve gone through the past several years.”
Another safety consideration in the design is its use of TRISO accident-tolerant fuel. TRISO fuel, 19.75% enriched, is structurally more resistant to neutron irradiation, corrosion, oxidation, and high temperatures than traditional reactor fuels. Saab expands on this: “We selected TRISO really because of the robustness of the fuel with uranium encapsulated by graphite. The coating on the TRISO fuel is carbon- and ceramic-based materials that prevent the release of fission products due to the higher melting point than uranium preventing the potential release risk. We chose it because of that technology and that safety ability.” He adds that many of the micro reactors and next generation SMRs have made the same design choice because of the robustness and the safety factors and is confident that fuel supply won’t be an issue despite the current lack of commercially available TRISO fuels. “There are a number of vendors out there working to manufacture TRISO, as well as Westinghouse which has got a fully vertical nuclear fuel supply chain. We’re assessing all options, either buy it or make it and we will have to evaluate to see what the best thing is for Westinghouse and our customers. We haven’t decided what that path would be as of yet,” he says. In any event, TRISO fuel is standardised so all the design and licensing requirements can be addressed before that decision becomes an issue.
The path to commercialisation
Westinghouse has revealed an ambitious time frame for both completion of the microreactor’s design and subsequent licensing and commercial roll-out. “We are aiming to have the design completed in 2028. Last November we announced our first customer, Saskatchewan Research Council. They would like to have an eVinci for their use in 2029. In, terms of licensing, we are working on both sides of the [US-Canadian] border right now. With the NRC in the US and with the CNSC in Canada where we’re going through the Vendor Design Review process. That is providing white papers and topical reports of Westinghouse efforts to get them familiar with the technology. That way when we do enter the formal licensing process, which will typically come from the customer license to prepare a site, likely Saskatchewan Research Council, then the regulator will be more familiar with the eVinci technology. For the NRC we’re doing the same and getting feedback on what’s working and what needs to be improved. We’re really putting ourselves in the best position for when customers start placing orders and we can be expedient through the licensing process,” says Saab.
Having achieved NRC and CNSC approval, the goal is to see an accelerated commercial roll out on the basis that it is a small unit and therefore potentially offers advantages in installation and commissioning.
As Saab says: “The benefit of a microreactor is they could be factory manufactured and taken to site. Essentially if the site is already prepped and ready with the infrastructure there our goal is to be able to make the connection and have it up and running in 30 days. Very different from a large capital construction of a gigawatt reactor.”
To facilitate serial manufacturing and a production line approach, Westinghouse already has plans in place, notably at the Etna facility near Pittsburg, Pennsylvania in the United States, which will be used for manufacturing all heat pipes for the demonstration unit as well as feature in the initial production of future commercial units.
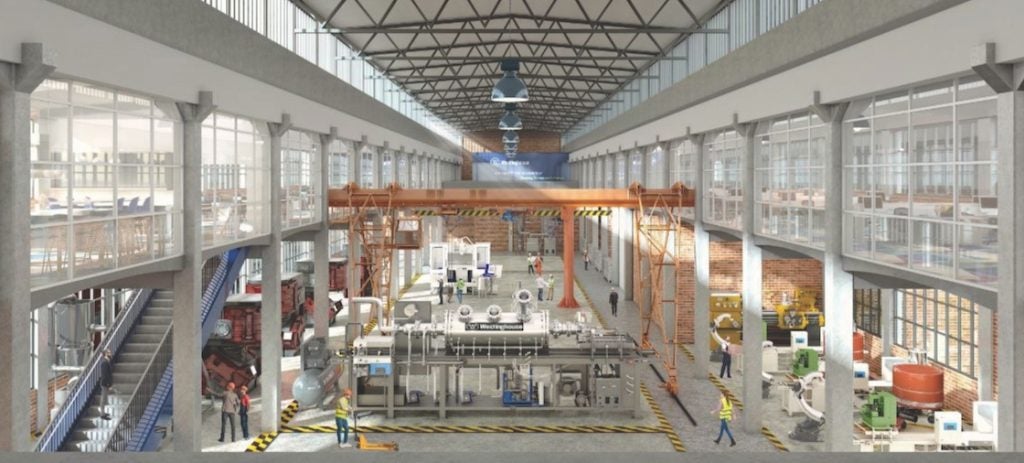
“We’ve made a significant investment in Etna,” says Saab, adding: “It’s also where the majority of the eVinci business unit team resides and that will be an accelerator hub for eVinci, where we will manufacture the first several units. As we get to fleet deployments and forecast out the demand for the technology, we’ll have to evaluate how to scale up manufacturing. That will be decided by our manufacturing team at the time.”
A modular model
The goal for the eVinci design will be transporting the fully manufactured unit to its operating location loaded with fuel. There it is expected to run for at least eight years before the complete unit will be returned to Westinghouse for refurbishment and refuelling. If required a replacement unit will be installed at the site simultaneously.
Saab explains: “We’ve designed the technology to be modular and envision about four, maybe five ISO containers for the system to be transported to site. We believe that the reactor itself will require a bit larger container, but will still be transportable through traditional methods. The goal has always beenl to design a technology that was transportable so that we can take advantage of manufacturing at scale. At the end of a fuel cycle we envision a swap out method, with no refuelling or handling of spent fuel at site. We would remove the reactor with the spent fuel and take it back to a dedicated site. If a customer needs continued operations we’ll probably need about 24 hours to do the swap out there. Otherwise, they can have pretty much uninterrupted power.”
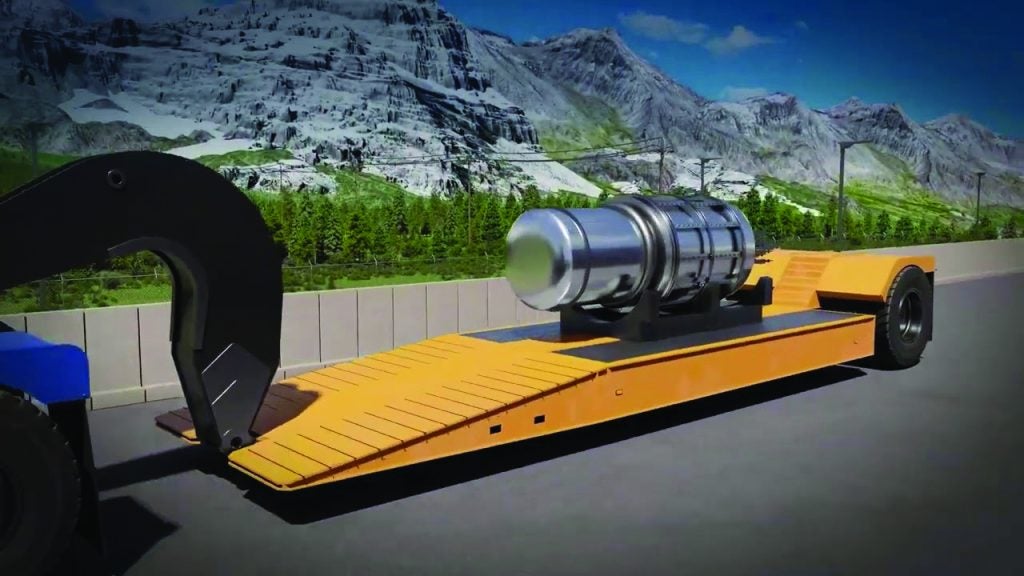
He continues: “In terms of the fuel, the plan is to bring it back to a Westinghouse facility and do the defuel and the refuelling and handle the waste management side of things. How we handle the transportation and the transport of a fuelled eVinci and a defuelled eVinci will really be dependent on the regulator in the specific country. That’s why we’re working really closely with the CNRC and the NRC to ensure that we meet all the requirements. We would do the same thing with the regulators in any other area as well. There are some nuances, but they’re all based on the IAEA regulatory requirements for nuclear power plants so there would be a lot of similarities.”
A wealth of applications
Refuelling cycles aside, the units are designed for at least 40 years of service life although some components will probably need to be refurbished after initial operations. As the next step in the development programme, Westinghouse will be installing a nuclear test reactor at the Idaho National Labs by 2026. This will be a scaled down version with a capacity of 1 MWe. “The nuclear test reactor will give us critical data, not only informing the design, but also licensing and lifespan,” says Saab.
Given the ambitious plans for that commercial eventuality there is clearly still significant work to do in validating the design of the reactor. Says Saab: “We’ve validated that the heat pipe technology can be scaled. We started with 4 foot [1 metre] heat pipes, and now we’re creating 12 foot heat pipes [4 metre]. Eventually for the full-scale design, the heat pipes will be just over 20 feet [5 metre].” Nonetheless, Saab acknowledges there are challenges that lie ahead: “I think one challenge will be overlapping the regulatory requirements for nuclear as well as the requirements for marine-based vessels. Timing will also be a challenge and also ensuring the process is commercially viable, finding the sweet spot between timing and cost is the key.”
Given that sweet spot is reached, Saab is optimistic that there are numerous applications that match the eVinci’s design outputs. “The luxury of what we’re developing is that the customer base is going to be quite broad. From remote industrial sites, data centres, communities, government installations, islands and island nations all requiring this nuclear battery. Although we’re proceeding this way because we’ve seen strong interests from the Canadian and the US markets, but we anticipate growth elsewhere too. We signed an MOU with ENEC, the Emirates Nuclear Energy Company, in the UAE, for instance and we’re discussing with additional customers and in other geographies. We do see eVinci supporting customers across Europe, to Africa, to the Middle East and even Australia when they lift their moratorium on nuclear. This will be a geographic solution for anyone requiring 5 MWe of clean, safe energy. And, if required and the end customer requires the heat as opposed to electricity, you can also get about 15 MW of thermal energy, that’s hot air at about 8000C. It is pretty dynamic technology that really allows nuclear to participate in areas that we’ve never participated before. Barge-mounted transportable EVINCI nuclear batteries will open the market to end users with siting challenges.”
A barge-mounted transportable plant is currently being developed in partnership with Canadian firm Prodigy Clean Energy. Westinghouse is working with the company on two projects, one marine or land-based and a grid-scale version installed at a shoreline within a protected harbour. In a related development Prodigy also recently signed a separate Memorandum of Understanding to explore potential TNPP projects with First Nations, Inuit, and Métis across Canada. The goal is to identify ways in which Indigenous Peoples could have ownership in the new generation of nuclear plants.
As Saab concludes: “It’s exciting to take our eVinci and find additional applications previously not able to leverage the many attributes of nuclear. Think of it as a battery pack, and our battery pack can be put on a barge, on piles on the shoreline, on a concrete pad and one day soon in space – it really depends on the customer and the environment and what the ultimate end need is.”