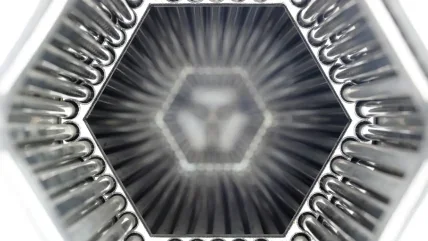
The nuclear fuel used in NPPs today has changed little since the initial deployment of nuclear power more than half a century ago. The fuel design for water-cooled reactors since the dawn of the nuclear power industry has been based on ceramic uranium oxide (UO2) fuel pellets, enriched to less than 5% U-235, contained in zirconium-alloy cladding tubes.
While continuous incremental improvements have been made on this basic fuel design, and modern commercial nuclear fuel outperforms the original fuel, modern fuel still consists of the same basic design elements of UO2 fuel pellets contained in zirconium-alloy cladding tubes. Incremental advancements in the performance of this fuel design may continue, but far-reaching advancements in commercial nuclear fuel performance will likely require fundamental changes.
Conversely, Lightbridge’s advanced metallic fuel rod design, being developed for use in existing water-cooled reactors and water-cooled SMRs, is fundamentally different than current fuel and offers a host of simultaneous step-change improvements.
Lightbridge metallic fuel rods are multi-lobed and helically twisted, consisting of a metallic uranium-zirconium alloy fuel core, that is co-extruded and metallurgically bonded to a zirconium-alloy cladding, and a central zirconium-alloy displacer that can be alloyed with burnable poisons.
The fuel core is an alloy consisting of approximately 50% uranium and 50% zirconium by weight. The uranium component of the fuel alloy can be enriched up to 19.75% U-235. Enrichment above 5% and below 20% is known as High-Assay Low-Enriched Uranium or HALEU. The cladding is composed of a zirconium alloy that is standard in conventional nuclear fuel. The helically twisted design provides self-spacing of the rods in a fuel assembly, eliminating the need for spacer grids.
Advantages of novel fuel
Because of its design features, the metallic fuel has inherently superior technical performance in several key areas compared to conventional cylindrical fuel rods consisting of UO2 pellets in zirconium-alloy cladding tubes:
- Lower fuel temperatures: Lightbridge metallic fuel has significantly higher thermal conductivity than ceramic UO2 fuel, and since Lightbridge cladding is metallurgically bonded to the fuel, there is no fuel-cladding gas gap as in conventional fuel rods. This results in Lightbridge Fuel operating at lower fuel temperatures, which translates into increased safety margins and better performance in normal, off-normal, and accident scenarios.
- Enhanced cooling: The multilobed, helically twisted design of the Lightbridge Fuel rods provides a significantly higher heat transfer area and greatly improved coolant mixing than cylindrical fuel rods. Since Lightbridge fuel rods are self-spacing and do not require spacer grids, they can accommodate increased coolant flow rates with lower pressure drop across the core. The use of the low pressure-drop Lightbridge Fuel is notably advantageous in SMRs that use natural circulation and passive safety systems.
- Use of HALEU: Lightbridge Fuel uses HALEU, containing adequate fissionable material to achieve power uprates, cycle-length extensions, and reach high burn-ups in light water reactors, reaching up to 50% or more burn-up beyond the current commercial fuel limits.
- Mechanical integrity of the cladding: Lightbridge Fuel utilises standard zirconium-alloy cladding material. However, unlike conventional pellet-in-tube fuel rods, the cladding is metallurgically bonded to the fuel and serves primarily as a barrier to fission product release instead of being the fuel rod’s primary structural component. As such, Lightbridge cladding is not subjected to the same mechanical stresses as in conventional fuel rods, allowing the fuel rod to maintain its mechanical integrity (both structurally and as a fission product barrier) to high burn-ups. Additionally, since the cladding is metallurgically bonded to the fuel, any breach of the cladding will only result in an isolated and localised amount of fuel being exposed to the coolant, reducing the consequences of a cladding breach.
- Mechanical integrity of the fuel: The fuel exhibits low swelling and excellent fission product retention in water-cooled reactor conditions, ensuring that the uranium-zirconium fuel alloy maintains its mechanical integrity and that low stresses are imparted on the cladding from the fuel. The co-extruded metallic fuel and cladding comprise a robust fuel rod design that withstands other mechanical loads from power transients, flow-induced vibration, seismic events.
- Proliferation resistance: The significantly reduced amount of U-238 in fresh Lightbridge metallic fuel contributes to improved proliferation resistance, since much less plutonium is produced during irradiation and it is in a proliferation-resistant isotopic mix.
- Reduced waste volume: Since Lightbridge Fuel can achieve high end-of-life burn-ups, the throughput of fuel required to operate water-cooled reactors (including for uprated power and extended cycle lengths) is significantly reduced, resulting in lower waste volumes.
These advantages inherent to the fuel design enable it to operate at higher power over longer time at lower fuel operating temperatures, with increased safety margins, while producing less waste that is more proliferation resistant than current fuel. The robust mechanical design makes it inherently better suited to withstand power adjustments, offering enhanced operational flexibility and enabling both large plants and SMRs to load follow.
Fuel development
The fuel design is an improved version of a mature fuel technology that incorporated uranium-zirconium fuel alloy composition and was used for decades in water-cooled maritime reactors. Improvements made in the design to optimise it for use in commercial water-cooled reactors include adding the central displacer to reduce fuel temperatures, using a modern nuclear fuel cladding alloy, and implementing the multi-lobed geometry for optimised heat transfer and coolant mixing. The maritime fuel used high-enriched uranium, and exhibited excellent performance to very high burn-ups, up to more than double the current end-of-life burn-up limits for commercial nuclear fuel. Since Lightbridge Fuel uses HALEU instead of high-enriched uranium, the expected burn-up levels are well within the experience base of maritime fuel, giving high confidence that it will demonstrate robust performance through its end of life in water-cooled NPPs and SMRs.
In support of future qualification and licensing efforts, the Lightbridge team together with several research institutions have conducted numerous studies, including simulation studies in a variety of conditions in various types of water-cooled reactors, thermal-hydraulic and vibration experiments, proof-of-concept irradiation testing of extruded multi-lobed fuel rodlets in a research reactor, as well as preliminary demonstration of manufacturing processes. Additionally, two GAIN Voucher awards enabled Idaho National Laboratory (INL) to design an Advanced Test Reactor (ATR) capsule irradiation experiment for the fuel, and Pacific Northwest National Laboratory (PNNL) performed casting demonstration work for manufacturing ingots of the fuel alloy using depleted uranium and zirconium alloy.
Lightbridge is currently conducting fuel development activities at INL, where the scope of work includes refinement of fabrication processes, irradiation testing of fuel material coupons, and corresponding post irradiation examinations of the irradiated materials. These studies will validate, under nuclear quality assurance standards, fundamental material properties during irradiation and are aimed to inform subsequent testing on rodlets under various conditions in the ATR and the Transient Reactor Test Facility (TREAT).
Additionally, two ongoing studies, funded through the US Department of Energy (DOE) Nuclear Energy University Program (NEUP) – one led by the Massachusetts Institute of Technology (MIT), and one led by Texas A&M University – are being conducted to investigate neutronic, thermal, and thermal hydraulic performance of the fuel in NuScale SMRs under normal and off-normal conditions, via simulation studies and laboratory experiments. These ongoing fuel development activities support the goal of licensing Lightbridge metallic fuel rods for use in existing NPPs and water-cooled SMRs.
Use in existing and future reactors
Lightbridge Fuel can be used in both existing nuclear power plants and small modular reactors designed to use conventional nuclear fuel, with no major plant modifications. In both cases, this enables step-change improvements in safety, fuel performance, waste reduction, and proliferation resistance. This leads directly to improved power plant economics, since the plant can produce more energy over a longer period between refueling outages, and operational flexibility is enhanced. For example, using the fuel in a four-loop pressurized water reactor (PWR) can enable a 10% power uprate and a fuel-cycle extension from 18 to 24 months, without the need for significant plant modifications.
In new-build reactors, including gigawatt-scale NPPs and SMRs, the balance-of-plant equipment can be designed to make optimal use of the advanced fuel that can enable power uprates of up to 30% above levels achievable with conventional fuel.
SMRs are designed to be faster to build, require a smaller upfront capital investment than large reactors, and aim to achieve economies of series production.
Use of the Lightbridge fuel in SMRs to increase power density while maintaining robust safety margins can also make them more economical and further enhance SMRs’ competitiveness with other energy sources.
In a future where the global installed nuclear capacity is dramatically increased to meet climate goals, it is likely that new installed capacity will consist of both gigawatt-scale NPPs and SMRs. Due to its ability to operate with high power density and its inherently robust design, the use of the Lightbridge fuel in future water-cooled NPPs and SMRs would require building fewer reactors to achieve the same installed capacity.
Lightbridge Fuel constitutes a significant advancement in water-cooled reactor fuel, offering improvements in safety, fuel performance, waste reduction, proliferation resistance, and power plant economics. It promises to set a new standard for nuclear fuel for water-cooled reactors.
Author: Dr. Scott Holcombe, Dr. Andrey Mushakov, and James Fornof, Lightbridge Corporation